Prerequisites
Before you start with the installation, you should check if your computer meets the requirements. Currently available computers should have no problems at all. If you have an old computer running Windows XP you may have difficulties. The Host works on Windows XP and later and on Linux. If you have a Macintosh computer, check for the Repetier-Host Mac on this site. All you need is .NET framework 4.0 or a recent Mono installation, if you are running Linux. The only other requirement is a graphic card with OpenGL. For a good rendering performance OpenGL 1.5 or higher is needed. With lower versions you may have speed issues with live preview.
Getting the software

Driver Advan Soulmate G4T; Asus Eee Pc 1001Pxb Notebook Bios; Hp Drivers Optiarc Cd Rw Crx880A Ata Device; Ethernet Driver For Axiz Cpu Windows Xp; Driver Ymf724F V Win7-32Bits; Free L40-18X Drivers Download; Pic Latency Tool Windows 7-X64; N35As1 Hyudai; Perfect View Webcam Driver; Shareport Utility 3-0 Mac; Sterownik Usb Thomson Lyra M150E. Automotive Features Ford® E-Series Chassis. Built to promote confidence behind the wheel, Axis RUVs are intentionally short Class A RVs. From behind the wheel of your Class a gas RV you can feel the power from the Ford® E Series 7.3 liter Triton® V-8 engine with 350 horsepower and 468lb.-ft. Of torque with Torqshift® 6-speed automatic transmission with overdrive. CALL OUR EXPERTS TODAY +27 (0)11-237-7000. © Copyright. Axiz (Pty) Ltd All Rights Reserved. Facebook Twitter LinkedIn YouTube Instagram.
Go to the download page and fetch the latest version for your os.
Windows installation
The windows version comes with a installer. After downloading run the installer and you are done. The installer already contains Slic3r and Skeinforge for slicing and python and pypy, which are needed to run Skeinforge.
Linux installation
The linux version comes as gzipped tar file. Move it to where you want your files and unpack its contents and run the post installation script:
After that you have a link in /usr/bin to the installation, so you can start it with repetierHost. Make sure you have all required Mono libraries installed. If you are in doubt, install Mono develop, which has all needed libraries as dependency.
One problem that most linux distributions have is, that the normal users are not allowed to connect to a serial console. You need to put your user into the right group. On Debian you can call:
to add your user to the group dialout.
First start
After the first start a dialog may pop up asking you, where your work directory should be. The latest windows versions skip this step, because the installer already created a work directory for you. You can select any directory, where you have write privileges, but it is advised to use a separate directory for this purpose.
The work directory is, where the host will put temporary stl files, sliced results and if enabled the log file.
Configuring your printer
The next step should be, to configure your printer so you can connect your computer with the host. Make sure your printer is connected and enabled. Some printer need special driver to access the device, so make sure the drivers are also installed. If you have uploaded the firmware to your printer, the driver is already installed.
Go to the menu “Config”->”Printer Settings” or klick the button . You will see a window like this:

At the top you see a drop down box, with the currently selected printer. At the start you have only the default printer. To create a new printer you only need to change the printer name and press “Apply”. The new printer will start with the same settings as the last selected printer.
Below the drop down box you see four tabs with most off the data stored with the printer configuration. In addition to this, for each configuration a start/end/pause/kill and five user defines scripts are stored with configuration. These can be changed in the g-code editor, which is described in a different chapter.
In this first tab, you set how to connect with your printer. In “Port” you select the port, where your printer is connected. At the opening of the window, all available ports were scanned and added to the list. If you connect your printer when this menue is already open, klick “Refresh Ports” to detect the new port. Select the right one. Then select the baud rate entered into the firmware. Stop bits and parity are correct for 99,9% of the printer, so leave them untouched.
The transfer protocol determines, how the host will communicate with the printer. All supported firmwares work in ASCII mode. The Repetier-Firmware also supports a binary format. The advantages of the binary format are:
- Reduced data size. Normal data is reduced to 50%.
- Better error correction.
- Less computation time needed for the firmware to parse the data.
You can leave this on “Auto detect”, which will automatically switch to binary format if Repetier-Firmware is detected. For all other firmwares, the ASCII communication is used.
The next decision is, how to send data to the firmware. The method that was planned with the first firmwares works like ping-pong. The host send a command and waits for the firmware to return an ok. This causes latencies, which can result in empty buffers if you have many small moves. To improve speed, you can allow the host to send more then one command at once. Your printer has a input buffer. As long as you are sending not more then the size of the buffer, you can send more then one command if they fit into the buffer. So if you disable the ping-pong mode, the host will send up to “Receive cache size” bytes, before it waits for the ok, telling him that the command is processed. If you are unsure on the printer buffer size select 63, which works on all printers. Firmware compiled with Arduino versions before 1.0 even allow 127 bytes.
The second tab defines important behavior you want. The Travel feed rate and Z-axis feed rate are used, when you move the extruder with the manual controls. The temperatures are set in the manual controls as start values. You can change them there any time.
When you turn the extruder on, you surely want to know the temperature of it. This is done by sending the M105 command to the printer. If you don’t plan to do this yourself every x seconds leave the option checked. You can also select how often you want the host to check the temperature. The default 3 seconds are a good start. With every request you get 2 entries in your log. The host will show the read temperature at the bottom in the status bar, so removing these messages from the log makes it much more readable.
Park position is where you like your extruder head the most. In the manual control you have a button to move the head to the park position. You can also tell the host to go to this position, after a print is finished.
The next check boxes define, what the printer should do, when a print is finished and if a SD card is available. If no SD card is available, the corresponding tab will not be displayed.
With “Add to comp. printing time” you define, how the host should correct the computed printing time. When the host computes the time from g-code, it assumes all moves are executed at the feed rate requested. If you do a slow print, this will be quite correct, except that it doesn’t take the time to heat the extruder/bed into account. With fast prints, the firmware needs to accelerate/decelerate a log, which increases the print time. After some prints, where you compared the computed and real printing time, you should be able to figure out how much percent you need to add to the computed time. Don’t expect to match every print. Depending on the geometry, the time will still differ a bit.
At the end you can change the moving direction in manual control for each axis.
In the “Extruder” tab you can define the numbers of extruders, the max. temperatures, that are shown in the manual control. The max volume per second defines the maximum amount of filament in mm³, the extruder can melt per second.
For each extruder you can define a name, a nozzle diameter (the diameter is only used for CuraEngine), a temperature offset, which is added to the filament temperature, if this extruder is selected (this also works only with CuraEngine), a color, which is used for preview, and x and y offset, which adjusts the extruder position for multi extruder prints. Some firmwares like Repetier-Firmware correct the offset themself, so in this case offset should stay 0.
The “Printer Shape” tab defines your printer shape, or to be more exact the shape of your build area. The host will use this to limit your moves and to check, if your models fit onto the print bed. You can also define the position of the x and y end stop.
The dump area is a rectangular hole in your print bed, where you can drop filament. Mostly the original Mendel had this. If you don’t have a dump area, leave the option unchecked.
If you like to add a visualization of your printer, you can design it with a 3d editor. Important points:
- You can have up to 3 stl files and assign each a different color.
- You need to export it, so that it fits bed position. The imported files do not get translated after loading.
- Sometimes it is useful to view the model from below. You can either decide to hide the printer if viewed from bottom or design you printer that you can view the model from bottom.
The last tab is for advanced configurations, you most probably will never need. Currently it only contains a post process filter. After the slicer is done with slicing, you can start an external program with the g-code. This program must save the resulting g-code in the file named by the #out parameter.
Units Settings
The host uses internally only millimeters. Unfortunately STL and OBJ format do not contain a scaling hint. Therefore you need to select the units used for the creation. That way the host will convert the units correctly into millimeters.
Categories: Shaft Alignment,Geometric Measurement,Machinery Diagnostics,Machinery Maintenance,Other Topics
X, Y, Z Axis. What do they stand for?
Everything must have perspective, a point of view, to be communicated. To communicate the three spatial dimensions, we use the X,Y, Z coordinates. These denote height, width and depth. In referring to machinery we use the same X,Y, Z denotations, but we give them different values or meanings. To make it even more interesting, there are no specific rules governing the meaning leading to confusion when attempting to communicate in these planes.
Figure 1, This is the “Hand Rule” used by the electrical trades to denote Thrust, Current and Field.
Figure 2, This is the “Right Hand Rule” used to denote the 3 axes.
Although the Right-Hand Rule shows the three axes, the spatial aspect is still not known in relation to a machine. This reference is used in the Machine Tool Trades. It is taught that the Z axis is referencing the vertical axis which is the center of rotation referred to as the axial plane.

Figure 3 This denotes the rotational axis of a CNC machine. This does not however denote a moniker of X, Y or Z. The direction of the thumb is referencing axial plane.
Knowing your axis reference is critical to understanding the information that is being conveyed. Your industry or trade may dictate the directional meaning. Figures 1-3 illustrates that knowing what the reference is, is like a key to a secret language known only by a select group. If you don’t have the key you may not understand the message.
Driver Axiom 25
Vibration analysis and precision shaft alignment are no different. They each have their own set of “rules” regarding the X, Y, Z axis that are task and/or tool specific.
Using a machine analyzer, such as the Fixturlaser Smart Machine Checker, the axis reference changes based on the position of the tri-axial sensor (accelerometer). The tri-axial sensor measures vibration levels in all three axes at once. This allows for many sensor position options. The only rule is that you must tell the display unit how reference mark on the sensor is positioned relative to the 3 axes by simply selecting the correct picture on the Smart Machine Checker display screen.
Figure 4, Note the sensor position reference in the top right corner. In this position, the X is Axial, Y is Radial Horizontal and the Z is Radial Vertical.
Figure 5, In this one the X is again Axial, but the Z and Y have reversed. Notice the sensor position reference in the top right.
When performing precision shaft alignment on horizontal rotating machinery, the Z axis refers to the rotational axis or rotational centerlines. The Y axis refers to vertical position (perpendicular to the base) and the X axis refers to the horizontal position (parallel to the base). As seen in Figure 6a below.
Axis P7216 Ptz Drivers
When aligning vertical rotating machinery, the Z axis is also the center of rotation, however X and Y are used to reference the two axial planes 90 degrees from each other as in Figure 6b.
Figure 6a & 6b
Another question that surfaces frequently during a horizontal shaft alignment is regarding positive and negative alignment values of the movable machine in relation to the stationary machine or reference shaft. Once again perspective or point of view is the key. When discussing the vertical position of the movable machine we typically say positive is up and negative down. +Y or -Y in Figure 6a above. Another way to say it may be positive is away from the base and negative is toward the base.
Axis Pad Controller Drivers
In the horizontal plane the positive and negative position (left or right) of the movable machine is again qualified by the point of view. When viewed from the back of the movable machine negative is to the left and positive is to the right of the reference shaft. -X and +X in Figure 6a above. This is the point of view when using Fixturlaser Shaft Alignment Systems.
Regardless of what trade or industry you are communicating (working) in, it is necessary that you know what plane is being referenced by each of the 3 dimensions to be able to correctly utilize the information you have gathered before taking corrective actions. Using incorrect references may lead to incorrect diagnoses of a condition or unclear communication of a problem or design between mechanics. Be sure to understand the reference before acting upon information regardless of the source.
Driving Axis
I really enjoyed but it would really help if I had a clear understanding of what is meant by the base. Thanks
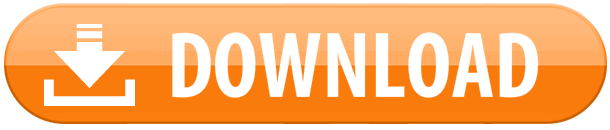